EHS Management System
EHS Management System
Scope
SAS implement environment, health and safety, energy management system (ISO 14001:2015/ISO 45001:2018/ISO 50001:2018)covers all activities, products and services of Chunan plant and Yilan plant. We actively enforce to improve the performance of EHS to ensure the effectiveness management system of EHS.

Certifications
ISO 45001:2018
Certificate No.:196466-2016-ASA-RGC-JAS-ANZ
Initial Certification Date: 11 March, 2016
Validity Period: 11 March, 2028
ISO 14001:2015
Certificate No.:196463-2016-AE-RGC-RvA
Initial Certification Date: 11 March, 2016
Validity Period: 11 March, 2028
ISO 50001:2018
Chunan Branch
Certificate No.:00001-2022-AN-TWN-TAF
Certification Date: 22 February, 2022
Validity Period: 21 February, 2028
ISO 50001:2018
Yilan Branch
Certificate No.:00004-2023-AN-TWN-TAF
Certification Date: 10 January, 2023
Validity Period: 9 January, 2026

Occupational Safety and Health Management System
In 2018, we have successfully switched from the OHSAS 18001 occupational health and safety management systems to the ISO 45001: 2018 system in all plants, with heightened focus on social expectations and managerial and staff participation. Occupational health and safety (OHS) is no longer regarded as an “independent operation” but has to be viewed from the angle of sound operation and sustainability. We adheres to the provision of safe and healthy work environments and modified pollution prevention and occupational hazards eradication, while conducting counselling with workers and their representatives, with the entire workforce made aware of individual liabilities and engaged in the environmental health and safety activities.
- Joint Responsibility for Work Safety and Safety Culture
SAS is fully aware of the importance of workplace safety. Since 2015, the company has been organizing “Work Safety and Safety Culture” activities to raise employees’safety awareness and strengthen employee literacy and discipline to ensure effectively decreased the occurrence of accidents. Starting from 2017, SAS launched the second stage of “Work Safety and Safety Culture” activities to achieve various KPIs including prevention of repeated mistakes and strengthening of autonomous safety management and employee safety concern to emphasize the importance of discipline and autonomous management. Employees are encouraged to actively report false alarm incidents and watch out for each other regarding workplace safety. The goal is to continuously strengthen employees’ safety awareness and enhance workplace safety.Our
current safety culture activity was upgraded to an occupational safety promotion program, which was launched in Q1 of 2023.The program is expected to kick-start safety management practices and gradual behavioral changes to effectively promote a safety culture, thereby eliminating occupational incidents.
- Contractor Management
SAS cooperates with a huge number of contractors in an effort to spur the industry development. We have formulated clearly defined contractor management guidelines to safeguard the health and safety of our partners and fulfill our pledge to provide a safe and healthy work environment.
When signing contracts with contractors, we request that they comply with OSH related laws and regulations and abide by relevant requirements of the company regardingpersonnel qualifications, construction work, machine tools and materials, and safety equipment. Accident occurrence rates are minimized through a series of management measures including pre-contracting and pre-construction hazard notices, construction application management by responsible units, access controls for contractors, management of construction operations, and post-construction verification in addition to sporadic on-site audits by health and safety management personnel in plant areas.
- Emergency & Contingency
There is usually not enough time to decide who should be responsible for what, how to do it, and how to obtain outside support when an emergency occurs. But failure to take effective control measures within a short period of time may lead to serious consequences. Conduct contingency drills for possible emergencies based on the plants’ hazard identification and risk assessment results. SAS has comprehensively reviewed and strengthened the fire/electrical equipment, electrical control measures, and related emergency response information in the plants such as shortening the emergency response drills frequency, integrating emergency response organizing personnel and emergency response equipment, handling a series of emergency response education and training, and building an information disclosure platform to enhance personnel awareness.
- Healthy Workplace
The physical health of employees is a key factor for the maintenance of work-life balance. Exceeding legal requirements, SAS has hired general practitioners to provide free on-site services including health consultation, guidance and assessment, as well as follow-up tracking health issues, referrals and medical services. In addition, SAS is firmly committed to the three pillars of maternal care, prevention of ergonomic hazards and prevention of burnout. The company safeguards the physical and mental health of our staff members through a wide range of health care initiatives, sporadic health talks, and health promotion activities in an effort to create a blissful and healthy work environment.
To ensure workplace environmental safety, starting from 2018, there have been installations of 24-hour Automated External Defibrillators (AED) inside the factories and arranged for 70% factory employees to attend CPR + AED education training so as to equip them with basic first-aid capabilities which can thus be applied on the site of incidents in a bid to construct a workplace conducive to employees health and safety. We are honored with the special safe workplace certification of safe workplace and the Badge of Accredited Healthy Workplace by the Ministry of Health and Welfare.
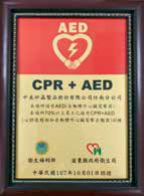
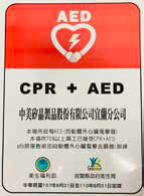
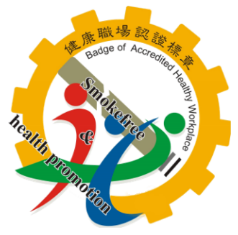
- Safe places / Badge of Accredited Healthy Workplace